The Importance of Energy Efficiency in Water and Wastewater Treatment – Case Studies
As those in the industry well know, water and wastewater treatment plants use an exorbitant amount of energy. In fact, 30-40% of total municipal energy consumption is due to water and wastewater treatment plants. In addition, energy currently accounts for 40% of drinking water systems’ operational costs and is projected to jump to 60% within the next 15 years. This excessive energy consumption places financial burden on already stressed water and wastewater utilities struggling to keep up with ever-increasing regulations and demand.
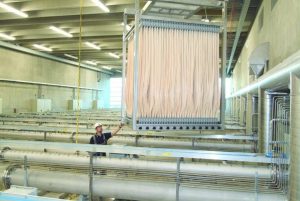
The Electric Power Research Institute (EPRI) conducted studies on wastewater treatment plants and cautions that as treatment requirements increase, energy requirements will also increase. EPRI also projects that as treatment requirements increase, the energy required to treat wastewater utilizing conventional technologies will increase exponentially. For example, new membrane bioreactor (MBR) processes actually consume 30-50% more electricity than plants that utilize more advanced treatment with nitrification. Also, plants that incorporate nanofiltration or reverse osmosis to meet stringent effluent utilize nearly twice the energy. EPRI further projects that strict nitrogen and phosphorus removal will be increasingly required, necessitating the incorporation of these energy-intensive technologies.
And let’s not forget the environment. Drinking water and wastewater systems add over 45 million tons of greenhouse gases annually, contributing to the already problematic issue of climate change. Bringing the issue full circle, climate change directly affects both the availability and the quality of our drinking water supply. The importance of incorporating energy efficiency into water and wastewater operations is paramount to these systems’ future sustainability.
Case Studies
Canaan, VT and Stewartstown, NH Shared Wastewater Treatment Plant Upgrades
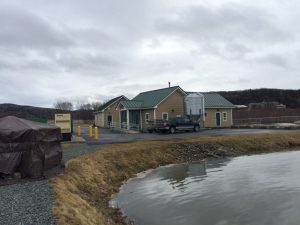
The Towns of Canaan, Vermont and Stewartstown, New Hampshire operate a shared wastewater treatment facility, which required significant upgrades. The existing facilities were 40 years old and although a few upgrades were performed in the 90s, the facilities were not performing well, did not meet Life Safety codes, and required significant maintenance.
One of the primary elements of the design was the consideration of the economics of energy reduction. The design incorporated insulated concrete form construction for the building walls with R-49 insulation rating in the ceilings. The design also included a wood pellet boiler with a pellet silo and hot water heating system, which allowed for reduction of explosion proof heaters in the headworks building. All of the windows were low-E and highly insulated, and an outer glassed-in entry way increased the solar gain retention of the building and reduced heat loss. The process headworks and operations buildings were constructed as single story structures, increasing operator safety. The lagoon aeration system is now a fine bubble, highly efficient process with additional mixing provided by solar powered mixers that help reduce aeration requirements, improve treatment, and allows for the addition of septage, all at no cost due to solar power.
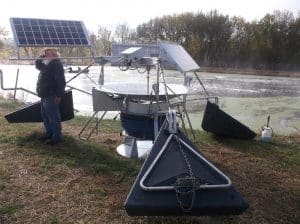
The pump station upgrades were designed to eliminate daily confined space entry by the operator by the conversion to submersible pumps. For sludge removal, a unique and simple “Sludge Sled” system was incorporated, which allows the operators to easily remove the sludge at their convenience. Sludge treatment is accomplished with a geo-bag system that allows the sludge to be freeze dried, reducing the volume by almost 50% with no energy consumption. The influent pump station was designed with three pumps instead of the normal two-pump system in order to meet both present and future design flows, allow for lower horsepower pumps, improve flexibility, reduce replacement costs, and reduce energy costs. The other four deep dry pit pump stations were converted to wet wells and submersible pumps, eliminating confined spaces, and are equipped with emergency generators, eliminating the need for operator attention when power is lost.
The incorporation of highly energy efficient building components resulted in reducing annual operation and maintenance costs, which resulted in a more sustainable facility. All of the equipment and processes were thoughtfully selected to reduce both annual and future replacement costs.
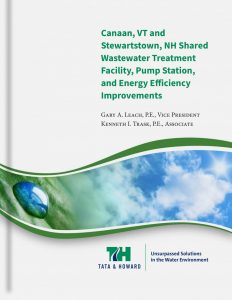
The treatment system is a 3-cell aerated lagoon system, and the solar powered mixers were installed to enable reduction of the aeration needs and horsepower during the summer months when septage is added. The aeration blowers, which are housed in insulated enclosures, reduce noise and were sized to allow for the addition of septage to the lagoons, which is not common in Vermont. The aeration blowers are controlled with Variable Frequency Drives (VFDs), which allow for greater operator control of aeration and provide energy cost savings. The operation is simple and safe for operators and others who need to maintain the facility and equipment. The design has provided flexibility to the operators and has resulted in an energy efficient, sustainable solution for this community.
Shrewsbury, MA Home Farm Water Treatment Plant Design
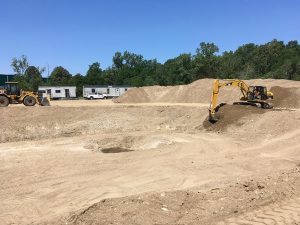
The Home Farm Water Treatment Plant (WTP) in Shrewsbury, Massachusetts was originally constructed in 1989. Although the WTP is still fully functional, its treatment capabilities are limited to chemical addition and air strippers for VOC removal, and the plant is capable of treating 6.0 million gallons per day (mgd). Manganese is present at all Home Farm wells, with widely varying levels from a low 0.03 parts per million (ppm) to a high 0.7 ppm. The existing treatment plant sequesters manganese, but does not have the ability to remove it from finished water.
Three treatment methodologies were piloted. The first two were greensand and pyrolucite, both commonly implemented catalytic media options for removing manganese and iron. The third was Mangazur®, a new technology. Mangazur® filter media contains the microscopic organism leptothrix ochracea, which consumes manganese and is naturally occurring in groundwater. Through consumption, the microbes oxidize the manganese to a state where it can precipitate onto the media. Unlike other media, Mangazur® does not require regeneration due to the continuous growth of microbes within the filter. Mangazur® technology also does not require chemical addition for pre-oxidation, minimizing the amount of chemical required for the plant.
Pilot testing for the biological treatment was performed over five one-week trials. Test parameters included a long shut-down on the filters, adding pre-oxidant, and adjusting pH or dissolved oxygen. The results of the testing indicated that although the Mangazur® does require a correct dissolved oxygen level and pH, it does not require a pre-oxidant, making the only chemical addition necessary for pretreatment potassium hydroxide for pH adjustment. Filter backwash efficiency is also a major benefit of the Mangazur® technology for the Home Farm application. With loading rates twice that of traditional catalytic media and filter runs exceeding 96 hours, the Town would only need to backwash the four filters once every four days rather than eight filters every day, saving a significant amount of water. The backwash flow rate and duration are also significantly lower for Mangazur® filters than for other traditional filter options. The results of the pilot tests indicated that all technologies were viable options to reduce manganese levels below 0.05 ppm; however, the biological treatment was the most efficient option.
Since the existing chemical feed equipment in the plant is aging and the existing building itself was also in need of rehabilitation, the decision was made to construct an entirely new standalone 7.0 mgd facility. The new facility will feature many energy efficient features including translucent panels for lighting efficiency, high efficiency water fixtures, high efficiency lighting, and stormwater bioretention areas for drainage. In addition, while the existing building will be demolished, the concrete slab slab will be kept for future installation of solar panels. The new facility also contains three deep bubble aerators for VOC removal. While Mangazur® technology has been approved in one other municipality in Massachusetts, there are few treatment plants in the northeast using this technology, and of those treatment plants, none have a design capacity above 5.0 mgd. Home Farm has a much higher design capacity and will be the largest Mangazur® water treatment plant in the northeast once completed. The Mangazur® filters at Home Farm will have the second highest design capacity in the country, after a 26.0 mgd treatment plant in Lake Havasu City, Arizona.
Download the complete whitepaper on the Mangazur™ Home Farms Water Treatment Plant here.
Flagstaff, AZ Water Reclamation Facility Upgrades
Tata & Howard provides on-call engineering services for water, wastewater, and energy related projects for the City of Flagstaff, Arizona. Several options for replacement of the blowers were evaluated and presented to the City in a report that recommended the installation of appropriately sized turbo blowers and upgrading the controls logic to automate dissolved oxygen controls.
The City had been experiencing long term maintenance issues with the existing biogas piping at the Wildcat Wastewater Reclamation Facility. The piping to the co-generator was not providing an adequate supply of gas from the digesters which, if operating, could save the City approximately $200,000 in annual power costs. The goals of this project were the restoration of the ability to run the generator on biogas, utilize the heat generated by the sludge digestion process to further reduce energy costs, reduce maintenance time to operate the biogas system, and have a positive impact on the environment, since methane is one of the most potent greenhouse gases.
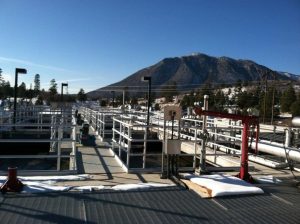
In addition, Tata & Howard conducted an energy efficiency study on the aeration blowers and pumps at two treatment plants. Pumping systems had efficiencies as low as 20%. Pumps and blowers were oversized to meet peak and future demands but not efficient at low flows or off peak flows. The testing showed that modifications to these systems had the potential to save the City approximately $250,000 in annual electrical costs and $445,000 in APS rebate funds for the modifications.
Download a case study on the energy efficiency project in Flagstaff, AZ here.
In Conclusion
While these three case studies are all extremely different projects, the goals are the same: increased energy efficiency, greener operations, and sustainability, all while meeting project objectives, budgets, and deadlines. Increasing energy efficiency in water and wastewater treatment is no longer optional; rather, it is a necessity to remain operational by meeting both budgetary and sustainability objectives. By incorporating innovative thinking and tailored methodologies into rehabilitation and repair projects, water and wastewater systems can ensure sustainable operations and a greener environment while protecting our world’s most precious resource for generations to come.
Thanks for pointing out that ensuring that the proper way of managing wastewater will ensure that our future will be sustained. I guess that is why my mom is looking for those who can offer this kind of service. This will be for the farm that she plans to open which will have lots of wastewater produces due to the cleaning of the stables and the water their animals need to drink in the future.