Private Sector — Legacy Farms
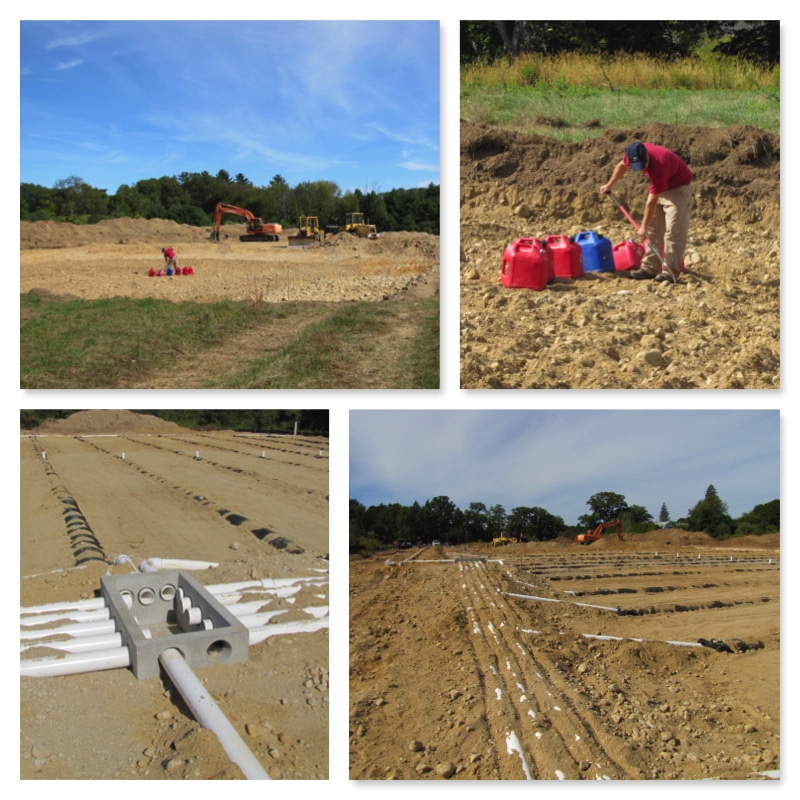
Tata & Howard provided design and construction administration services associated with expansion of the Legacy Farms private wastewater treatment facility and effluent disposal areas.
The project assisted in moving from 115,000 gallons per day (gpd) to 190,000 gpd, which consists of the installation of additional membrane cassettes to increase the capacity from 115,000 gpd to 150,000 gpd, installation of additional membrane modules, installation of mechanical equipment fully redundant at a maximum daily flow of 190,000 gpd, permitting assistance with MassDEP, and the construction of two additional effluent disposal areas. Construction of the first of two new effluent disposal areas is underway, and T&H Project Engineer and Certified Soil Evaluator Matt Barry was recently on-site to conduct a perc test for the second effluent disposal area.
Original Project
Tata & Howard provided soil investigation and evaluation, preliminary design, and design services for an onsite wastewater treatment facility and disposal system to serve the proposed Legacy Farms mixed-use development in Hopkinton, Massachusetts.
The Legacy Farms development includes a retail village, a commercial district, a variety of residential spaces (apartments, town homes, single-family homes, and multi-family structures) on approximately 733 acres currently used for nursery and agricultural uses. Approximately 940 new dwellings, 450,000 square feet of retail and commercial space, and 500 acres of restored open space will be made available by the project.
Tata & Howard’s services have included development of treatment flows for the full, built-out project, as well as selection and design of the wastewater pumping treatment and disposal systems that were compatible for the site configuration and soils, and that would provide the level of treatment required by the Massachusetts Department of Environmental Protection (MassDEP). The challenge was satisfied by the design for a phased approach to the construction of a membrane bioreactor (MBR) treatment system, which provides a high level of treatment.
The project includes three submersible pump stations that serve the wastewater treatment facility (influent, recirculation, and effluent disposal) and two submersible pump stations within the development itself.
Disposal of treated effluent at the Legacy Farms site will be managed by a combination of conventional leaching systems and an innovative use of drip irrigation, the first large-scale application of drip irrigation for disposal of treated effluent in the State of Massachusetts.
The success of this project was related to excellent communication between Tata & Howard and the client, and a strong working relationship with MassDEP.