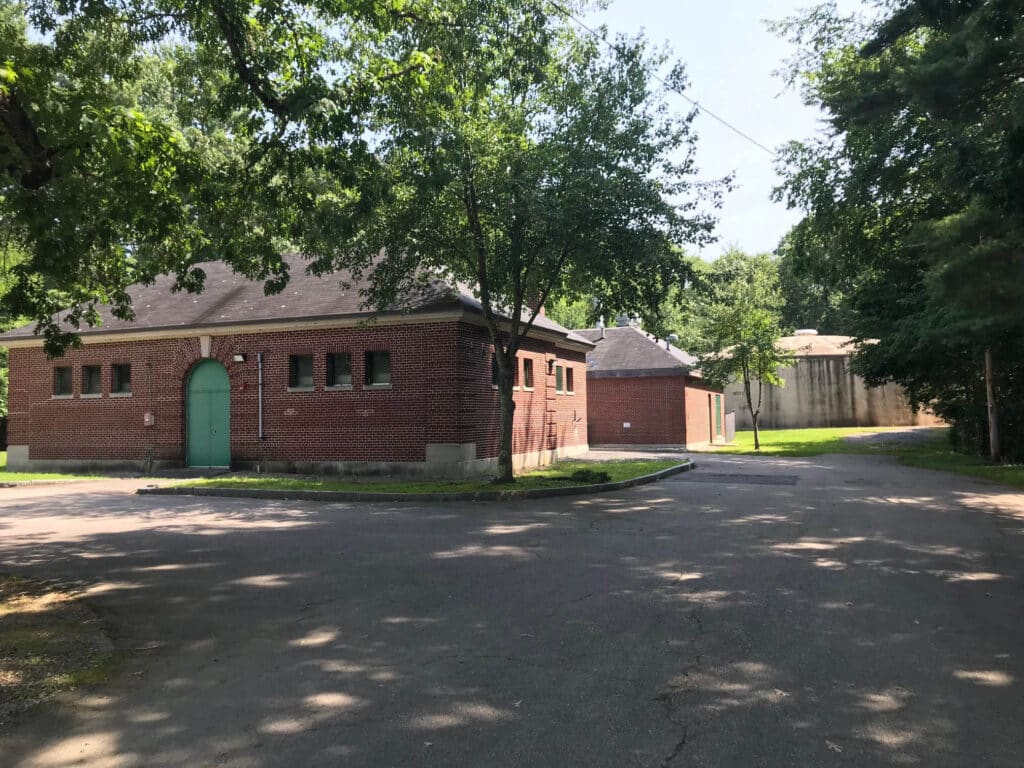
At the Wading River Water Treatment Plant, pilot testing, conducted by Blueleaf, Inc. and consulted by Tata & Howard, Inc., was performed to evaluate the removal of natural organic material for the reduction of disinfection byproduct formation in the distribution system, the reduction of manganese concentrations, and the removal of PFAS compounds. The removal of organic carbons by magnetic ion exchange (MIEX®), the removal of manganese by GreensandPlus™ filtration, and the removal of PFAS by FLOURO-SORB®-200 media, were found to be the most effective treatment processes.
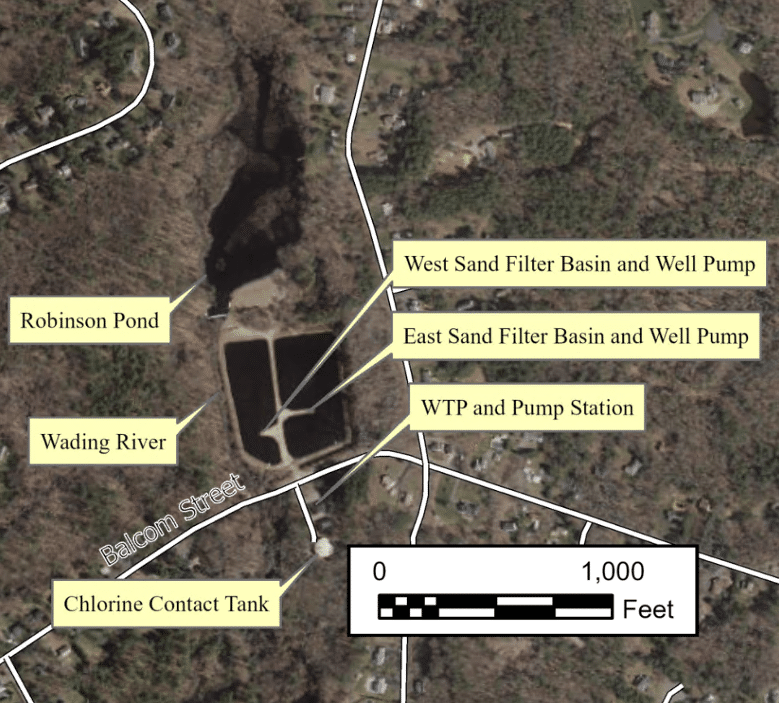
Project Background
The City of Attleboro, Water Department (AWD) operates the Wading River Water Treatment Plant (WTP), located in Mansfield, MA, which includes two gravel packed supply wells and submersible well pumps, each pumping from a filter sand bed. The Wading River provides additional water to the filter sand basins via a steel pile dam and intake structure, and is considered a surface water source. The wells pump to the WTP where water is chemically treated with sodium hydroxide for pH adjustment, sodium hypochlorite for disinfection, polyphosphate for corrosion control, and hydrofluorosilicic acid for dental hygiene. Treated water flows through a 630,000-gallon, baffled concrete contact tank prior to being pumped into the water distribution system.
The Wading River source is historically a high source of organic matter, which act as disinfection byproduct (DBP) precursors in the distribution system. Despite efforts by the City to optimize existing treatment to reduce the formation of trihalomethanes (TTHMs), a class of DBPs, test results have indicated levels above the maximum contaminant level (MCL) of 80 micrograms/liter (µg/L) in some quarters, with locational running annual averages (LRAA) up to almost 85 µg/L at some sampling locations. To reduce DBP precursors and operate the WTP year-round, targeted treatment for organics removal will be required.
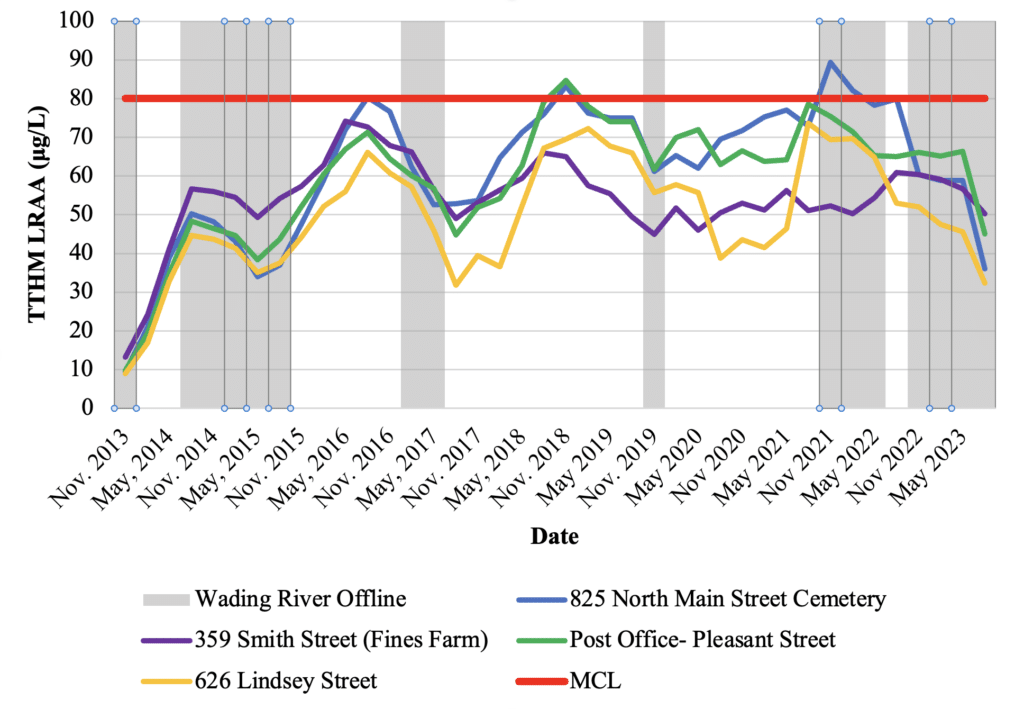
The Massachusetts Department of Environmental Protection (MassDEP) published a new combined MCL of 20 nanograms/liter (ng/L) for six perfluoroalkyl and polyfluoroalkyl compounds (PFAS) in October 2020. Following the publication of the new standard, testing for PFAS was conducted at the Wading River supply wells and the Wading River WTP finished water in September 2020, October 2020, January 2021, and monthly from April 2021 to September 2021. Laboratory results indicated PFAS results over the limit, suggesting a need for targeted treatment.
MassDEP guidelines require the completion of a series of permit applications and an engineering study including a pilot test proposal, pilot testing, and a pilot test report to evaluate, optimize, and summarize the treatment results. In accordance with those guidelines, three seasons of pilot testing were conducted: Season I, from March to April of 2022, Season II, from August to September of 2022, and Season III, from July to August of 2023. Per the standards to conduct a pilot study on surface water sources, the pilot test included one cold weather season and one warm weather season.
Pilot Testing
Two systems for organics removal were tested: 1) dissolved-air flotation (DAF) followed by dual-media filtration, and 2) magnetic ion-exchange (MIEX®) followed by GreensandPlus™ filtration. The MIEX® & GreensandPlus™ filtration process train was added to the pilot test following the discovery of elevated manganese levels during Season I of testing.
DAF clarification is a process similar to clarification by sedimentation, except that particles formed by coagulation are floated to the surface by the injection of air through a recycle stream at the bottom of the clarifier tank, instead of being allowed to settle to the bottom. The recycle stream is injected through specially designed nozzles, resulting in the formation of bubbles which adhere to formulated flocc particles and float to the surface, effectively clarifying the source water. Depending on the system utilized, typical DAF systems can operate with a surface loading rate of between 4 and 8 gallons per minute per square foot (gpm/sf). Optimal coagulation and flocculation conditions for DAF can be predicted by standard jar tests, which were conducted prior to Season I of testing. Polyaluminum chloride (PACI) was selected as the coagulant.
Dual-media filtration is a gravity operated, rapid-flow process widely used in water treatment. It is necessary to follow the coagulation, flocculation, and clarification processes with filtration to remove excess turbidity. Dual-media filters contain a layer of anthracite on top of a layer of fine sand, which rapidly remove residual solids from the water, trapping larger particles in the anthracite and smaller particles in the fine sand. The filters can be backwashed on a schedule determined by differential pressure across the filter or at periodic time increments.
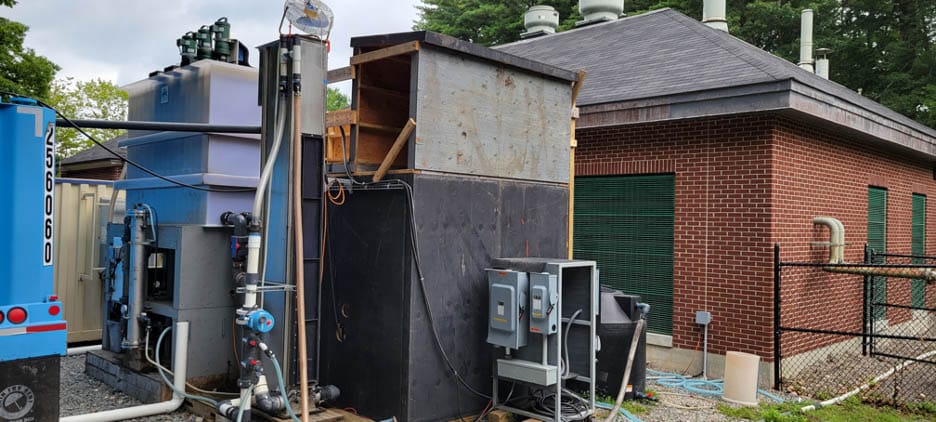
MIEX® is a specialized treatment process targeted at the removal of organic carbon, specifially dissolved organic carbon (DOC). MIEX® resin consists of ion exchange beads that contain magnetized components to form agglomerates from negatively charged organic particles. The MIEX® system utilizes a stirred up-flow contactor, resin settler, and a regeneration/recycle loop to remove total organic compound (TOC) in an efficient manner. Batches of resin are periodically regenerated in a sodium chloride brine solution, replacing the TOC with target chloride anions and leaving a concentrated brine and organics waste stream. Freshly regenerated resin, as well as new resin to make up for carryover losses, is fed to the reactor to maintain a consistent ion exchange capacity. Depending on the system utilized, hydraulic loading rates can range from 6 to 12 gpm/sf. Residuals from MIEX® systems consist of waste from the regeneration process, and depending on the frequency of regenerations, are typically 0.02% to 0.06% of the treatment flow.
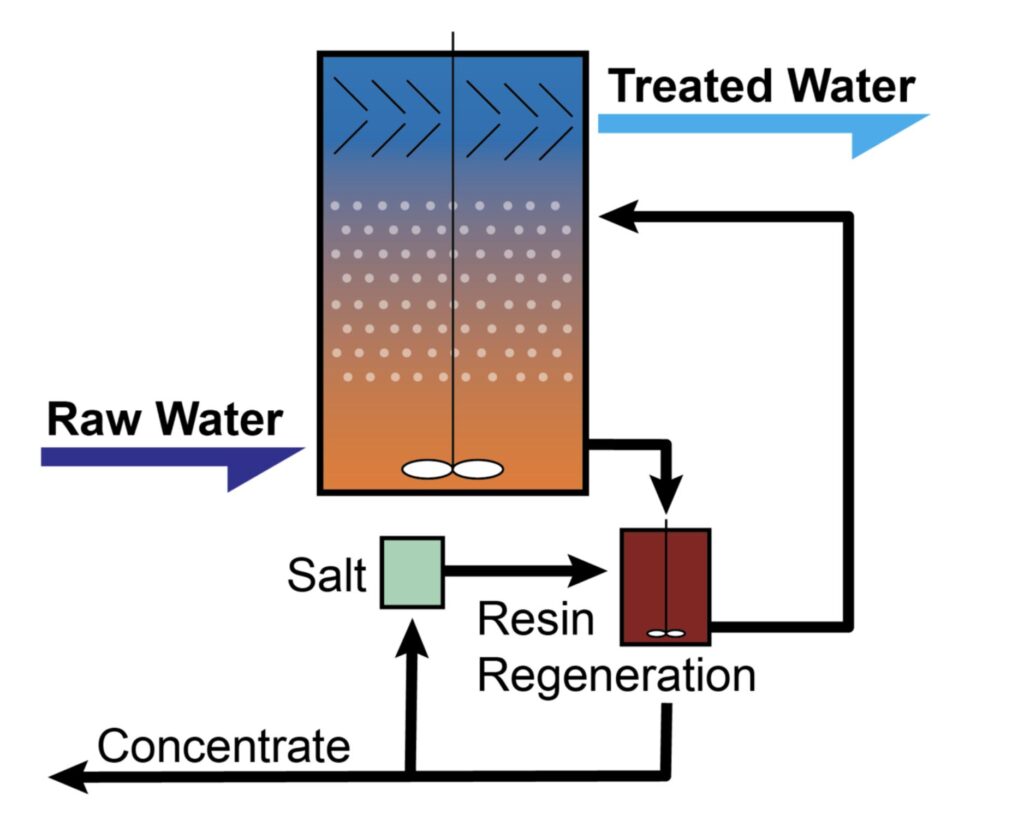
GreensandPlus™, the trade name for Inversand’s oxide-coated sand product, is a manufactured filter media used for the removal of iron, manganese, hydrogen sulfide, arsenic, and radium from water supplies. The GreensandPlus™ process utilizes a layer of anthracite which acts as a physical filter for the manganese precipitated by the addition of the chlorine oxidant. Below the anthracite top layer is the oxide-coated sand media, which acts as a catalyst in the oxidation of the manganese. Manganese that is oxidized in this part of the process is then removed via adsorption or physical filtration.
For PFAS removal, two treatments were compared: 1) granular activated carbon (GAC) and 2) an anion-exchange removal, clay bentonite media, FLOUROSORB®-200.
GAC filtration has proven to be effective in removal of PFAS from drinking water at many locations throughout New England. GAC removes PFAS by adsorption, which is a physical process of accumulating a substance at the interface between the liquid and solid media phases. The GAC used in this pilot study was Calgon FILTRASORB 400, which is made from select grades of bituminous coal through a process known as reagglomeration to produce a highly active, durable, granular product capable of withstanding the abrasion associated with repeated backwashing, hydraulic transport, and reactivation for reuse. The Calgon FILTRASORB 400 can be recycled and reused through thermal reactivation to restore its adsorptive capacity, which eliminates the costs and long-term liability associated with the disposal of spent media.
CETCO’s FLOURO-SORB®-200 is a proprietary, NSF-certified, bentonite-clay adsorption media that is proven to effectively treat multiple variants of PFAS. The removal mechanism is similar to anion-exchange resins. FLOURO-SORB®-200 adsorbent media binds the entire spectrum of PFAS compounds, is not negatively impacted by most other water quality parameters such as dissolved or total organic carbon and chlorine and requires short empty bed contact times of two to three minutes.
Removal of Organic Compounds and Manganese
As mentioned previously, manganese concentrations were found to be higher than expected during Season I of testing. The first organics removal process, DAF and dual-media filtration, was utilized to remove manganese by several oxidation strategies. The oxidation of manganese causes it to precipitate out of solution, allowing it to be removed by direct filtration through the dual-media filters. The oxidation strategies included the oxidation of manganese by potassium permanganate, sodium hypochlorite, and chlorine dioxide. While potassium permanganate was the most effective oxidation chemical for direct filtration of manganese, none of the oxidation strategies were able to consistently maintain manganese concentrations below the secondary maximum contaminant level (SMCL) of 0.05 mg/L. Additionally, DAF followed by dual-media filtration did not consistently reduce DBP precursors to maintain TTHMs below the MCL of 80 μg/L in simulated distribution system sampling.
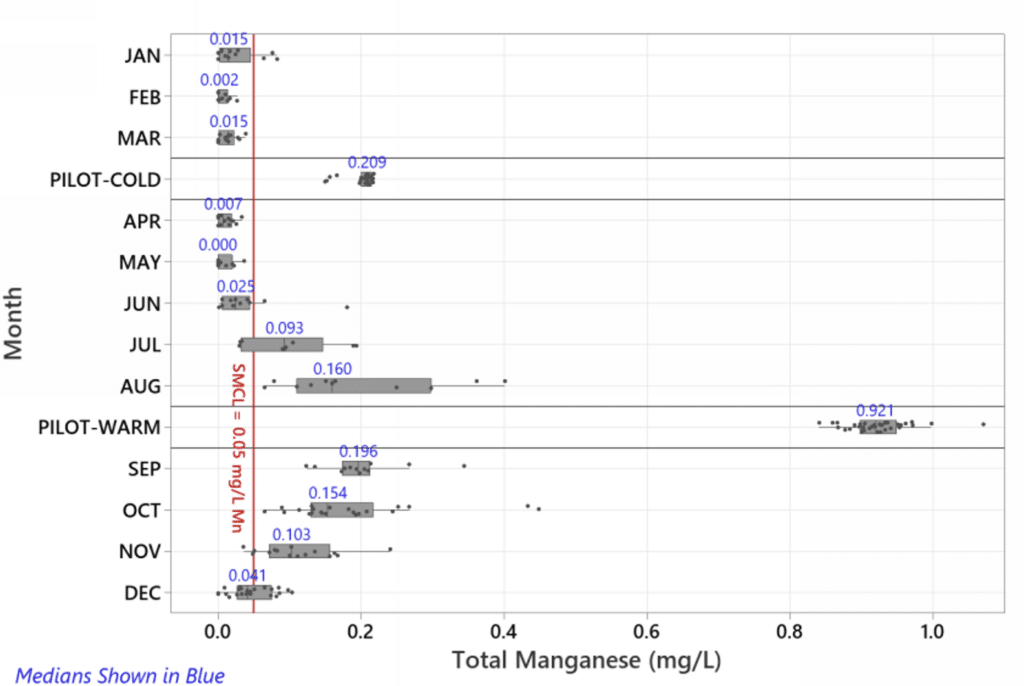
While GreensandPlus™ is more effective than dual-media filtration for manganese removal, providing additional oxidation of manganese with its oxide-coated media, the coagulated particles formed by DAF can be problematic for GreensandPlus™ media, “gumming up” the small particles with coagulant and reducing filter run times. Therefore, MIEX®, which does not coagulate organic particles for removal, was provided as an alternate pretreatment for the removal of organic compounds prior to manganese removal. MIEX® followed by GreensandPlus™ filtration was found to be effective for both organics and manganese removal, maintaining manganese concentrations below the SMCL, and removing DBP precursors to reduce TTHMs below 80 μg/L in simulated distribution sampling.
Removal of PFAS
Since many media have been shown to remove PFAS to non-detect levels, one way to measure the relative effectiveness of PFAS removal by a particular media is in terms of empty bed volumes (EBVs) between media replacement. By measuring PFAS breakthrough (defined as PFAS being higher than non-detect levels) at sampling points located 25%, 50%, 75%, and 100% through the treatment beds, EBVs for each treatment option were estimated. After 16 weeks of PFAS testing, GAC had treated almost 14,000 EBVs, and was providing 23% PFAS removal at the 25% tap, 41% removal at the 50% tap, 69% removal at the 75% tap, and 90% removal at the 100% tap. At the same time, FLOURO-SORB®-200 had treated approximately 68,600 bed volumes, and was providing 87% removal at the 25% tap, 85% removal at the 50% tap, and 100% removal at the 100% tap. The FLOURO-SORB®-200 media was determined to have a higher treatment capacity than GAC for PFAS removal.
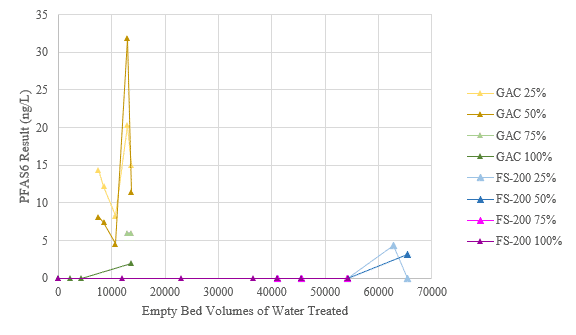
Conclusions
The DAF and dual-media filtration treatment process was utilized throughout the study to evaluate TOC removal and manganese removal by coagulation, oxidation, clarification, and filtration. A MIEX® and GreensandPlus™ treatment process was added during Seasons II and III as an alternate for TOC and manganese removal. Both processes were found to be effective in removing TOC, however, the MIEX® & GreensandPlus™ process was more effective than the DAF & dual-media filtration process in removing TOC and reducing DBP formation. Additionally, the MIEX® & GreensandPlus™ process more consistently removed manganese to concentrations under the SMCL than the DAF & dual-media filtration process. FLOURO-SORB®-200 clay bentonite anion-exchange media was found to have a higher capacity for PFAS removal than GAC. FLOURO-SORB®-200 showed significantly more bed volumes treated before PFAS breakthrough at the 25% and 50% taps than GAC showed at breakthrough of the equivalent sample tap, making it a more effective treatment media for removal of PFAS.