In honor of International Beer Day, we are taking a look at what breweries are doing to conserve the number one ingredient in brewing beer: water. Due to water shortages, increased demand, and heightened awareness, many breweries have taken steps to increase water efficiency and to implement water saving techniques in their brewing. Utilizing a myriad of methodologies and technologies, an increasing number of today’s breweries have begun to focus on brewing beer with water efficiency and conservation at the forefront of their business.
Anheuser-Busch InBev
The undisputed behemoth of the beer world with 25% of the global beer market, Anheuser-Busch InBev has implemented water-saving measures in many ways. Some of its plants use reclaimed water for equipment cleaning, irrigation, firefighting, and other local uses, such as watering a soccer field in Peru and manufacturing bricks in Brazil. And, as would be expected from such an enormous, influential company, Anheuser-Busch InBev is piloting agricultural programs that it hopes will spread to all facets of agriculture. To start, they have initiated a “Smart Barley” program with 2,000 barley growers in Idaho and Montana. Since agriculture accounts for 95% of the water used in beer making, increasing agricultural water efficiency is the key to breweries becoming better water stewards. Utilizing sensors in the field, cooperative programs, and its own hybridized, drought-resistant seeds, Anheuser-Busch InBev hopes to decrease agricultural water usage by 25% over the next two years.
Even before the implementation of its agricultural program, Anheuser-Busch InBev had managed to reduce its water footprint to the point that it now uses less water than any other major brewer. As of this writing, the company uses about 3.2 bottles of water for each bottle of beer, and the industry average is seven bottles of water per each bottle of beer. In fact, from 2013-2014, Anheuser-Busch InBev saved as much water as is used in the manufacture of four billion cans of Budweiser.
MillerCoors
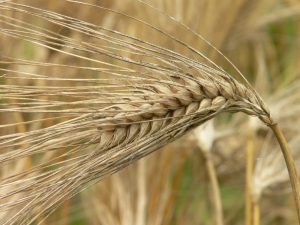
MillerCoors is also a giant in the beer industry with 30% of the American beer market. Like its major competitor Anheuser-Busch InBev, it also has an Idaho-based pilot project called the Showcase Barley Farm in Silver Creek Valley, Idaho. Utilizing precise irrigation techniques and hardier crop planting, MillerCoors is researching the best ways to increase its water efficiency. Already a success in 2011, Showcase Farms saw a 9% reduction in water usage by precision irrigation alone.
MillerCoors has also implemented water efficiency and conservation measures at its breweries such as utilizing recirculated water rather than freshwater for cooling, reusing wastewater for non-potable uses, cleaning cans with ionized air rather than water, sanitizing systems with bleach instead of hot water, and installing waterless lubrications throughout their operations. The water reclamation system in their Milwaukee brewery alone saves 100 million gallons of water per year. The company uses 3.53 bottles of water for each bottle of beer it produces — just a tad more than Anheuser-Busch InBev — but it hopes to slash its water footprint an additional 15% by 2020.
Both Anheuser-Busch InBev and MillerCoors have made huge strides towards water efficiency, and because of their massive size, the impact is significant. However, many smaller craft breweries are doing just as much — and in many instances, more — to become water and environmental stewards.
Full Sail Brewing Company
Oregon-based Full Sail Brewing Company is fully committed to water conservation. They operate a hot water recovery system that saves over three million gallons of water per year. Employees work four ten-hour days, which saves another three million gallons of water per year. They have installed special filters to maximize malt extract while minimizing water usage, they’ve reduced spray nozzle apertures on bottle and keg washers, and they’ve reduced cooling water usage by adding a glycol chiller in tandem with their heat exchanger. These measures save an additional 4.1 million gallons per year. The result? The forward thinking company uses just 2.5 bottles of water for each bottle of beer produced — the lowest ratio we have found. But they don’t stop there. Full Sail Brewing operates its own voluntary wastewater treatment plant, which reduces the load to the municipal treatment plant by pre-treating the wastewater. In addition, they distribute their treatment plant’s biosolids to local farmers and an orchardist for fertilizer.
Cape Cod Beer
Hyannis, Massachusetts-based Cape Cod Beer utilizes water reclamation and conservation efforts in their brewing, but they take it a step further. Their beers are only sold in refillable kegs or growlers, and they are passionate about recycling. In addition, they donate all used and leftover grain to local farmers for feed or compost, and they were recently certified “Cape & Islands Green” Level 1.
California Brewers
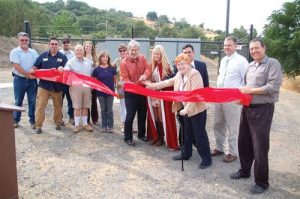
The City of Cloverdale celebrated the completion of two new wells during a ribbon cutting
Bear Republic Brewing Company, whose corporate office and larger brew house are located in Cloverdale, California, actually partnered with the City of Cloverdale to dig two new water wells, which went online last August. Because the City didn’t have the funds for the new wells, Bear Republic prepaid several years of its water fees — $466,000 — in order to allow the city to complete the project on time and under budget. Bear Republic also conducts regular audits for leaks, practices conservation and reclamation in its operations, and is installing a wastewater pre-treatment plant that will generate heat and electricity with the methane it produces as well as reclaimed water for irrigation and cleaning.
In Escondido, California, the nation’s tenth largest craft brewer, Stone Brewing Company, treats all of their brewing wastewater — not to be confused with restaurant or restroom wastewater — with an aerobic digestion and filtration process. The reused water is pure and they use it for cleaning. “From a good brewing practices standpoint, it’s good to watch water usage, especially when you live in a dry area like we do,” explained Mitch Steele, Stone’s Brew master. He also added that they test the reclaimed water frequently and that, if regulations allowed, he wouldn’t hesitate to drink it.
Adding to their already environmentally friendly business practices, both Stone Brewing and Bear Republic have been proactive in sharing their practices and knowledge with the rest of the craft beer community through webinars and on-site tours.
Brewers for Clean Water
So far, over 50 craft breweries, including eight New England breweries, have joined the National Resource Defense Council’s Brewers for Clean Water initiative. The program aims to spread awareness of the Clean Water Act and to support initiatives that protect and conserve our nation’s water. “As we continue to see the craft beer segment grow, we as brewers owe it to the communities we live, work, and play in to be mindful of protecting our waterways as we strive for growth that is environmentally and socially responsible now and down the road,” said Mat Stronger of Allagash Brewing Company, a Portland, Maine-based brewery that is active in the Brewers for Clean Water initiative.
Jester King Brewing with Harvested Rainwater
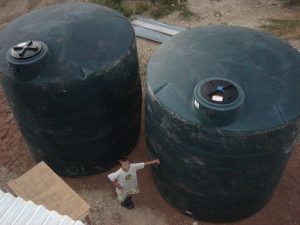
Austin, Texas-based Jester King Brewery recently purchased 3,000-gallon rain water collection tanks that will collect rainwater from the roof of both their brewery and adjacent beer hall. They expect to capture an estimated 10,000 barrels of rainwater per year that will be disinfected using ultraviolet and reverse osmosis purification and then be used in their brewing process.
Beer Made with 100% Reclaimed Water
Clean Water Services, a wastewater treatment utility that serves the Portland, Oregon metro area, asked for approval from the state to allow members of the “Oregon Brew Crew” to use recycled sewage water from its Forest Grove plant for beer-making. They received initial approval from the Oregon Environmental Quality Commission and the Oregon Health Authority, but will need further approval for a recycled water reuse plan before forging ahead. Last year, the Oregon Brew Crew produced test batches of beer made from 30% reclaimed water, which met with rave reviews. But, according to the dozen brewers, using 100% reclaimed water will be a more exciting challenge.
“I’m trying to think of a really cool recipe. When they told us 100 percent we’re like oh man, first the names, then the recipe comes later. And I’m excited,” said Lee Hedgmon, president of the Oregon Brew Crew.
Clean Water Services believes that educating the public about recycled water will lead to its ultimate acceptance, and they don’t think there’s any better way to start that conversation than with beer.
Sewage Beer
Really. It’s called Activated Sludge, has a radiation symbol on its label, and is brewed with purified Milwaukee Metropolitan Sewerage District wastewater plant effluent that has NOT gone through the final cleaning process typically necessary for potable reclaimed water.
Theera Ratarasarn, a wastewater engineer with the Wisconsin Department of Natural Resources, enjoys home-brewing beer to relax after his two young sons have gone to bed. After doing some thinking, he decided he wanted to raise awareness of the quality of plant effluent, and figured the best way to do so was with his evening hobby.
“I wanted to get people talking,” he said “There’s a potential use for what we discharge into lakes and streams.”
Ratarasarn filtered, treated, distilled, and tested the water before beginning to make five gallons of his Activated Sludge, a wheat ale with 5.15% alcohol by volume. And then came the true test. Ratarasarn presented his sewage brew to a taste panel at Lakefront Brewery, where Activated Sludge competed against Lakefront Wheat Monkey. The result? “It’s one of the better home brews I’ve ever had,” stated Mitchel De Santis, who graded the beer a seven out of ten.
“Everybody I talk to wants one,” added Ratarasarn.
Brewing Up Water Efficiency
Breweries are some of the largest consumers of water, yet have proven that they are some of the most active conservationists. We’ve heard it before: everyone loves beer, so it is an easy way to spread awareness, start conversation, and implement efficiency and conservation techniques. While we may not be drinking sewage beer any time soon, we can all agree that U.S. breweries are doing their part in the water conservation effort — and that’s something to which we can raise a toast. Happy International Beer Day!