Have you thought lately about the overall health of your business? In today’s economy, it’s important to not only deliver your service, but to operate effectively and efficiently. An excellent way to gain insight into this is through conducting a Business Practice Evaluation (BPE). A BPE assesses the health of a utility by developing the framework for a structured approach to managing, operating, and maintaining assets in a more business-like manner. The goal would be to minimize the total cost of operating, managing and maintaining utility assets while still delivering exceptional service to customers. This is accomplished by providing more effective preventive maintenance to reduce capital investment.
The evaluation process will ultimately enable utility managers to assess the efficiency and effectiveness of their business practices in comparison to industry standards. Developing system specific plans, programmatic approaches, and realistic timelines to optimize utility programs are included in this process.
Similar to management consulting services, a BPE has potential to bring incredible value to your utility. While the list of benefits is copious, here are a few of the major advantages of conducting a Business Practice Evaluation.
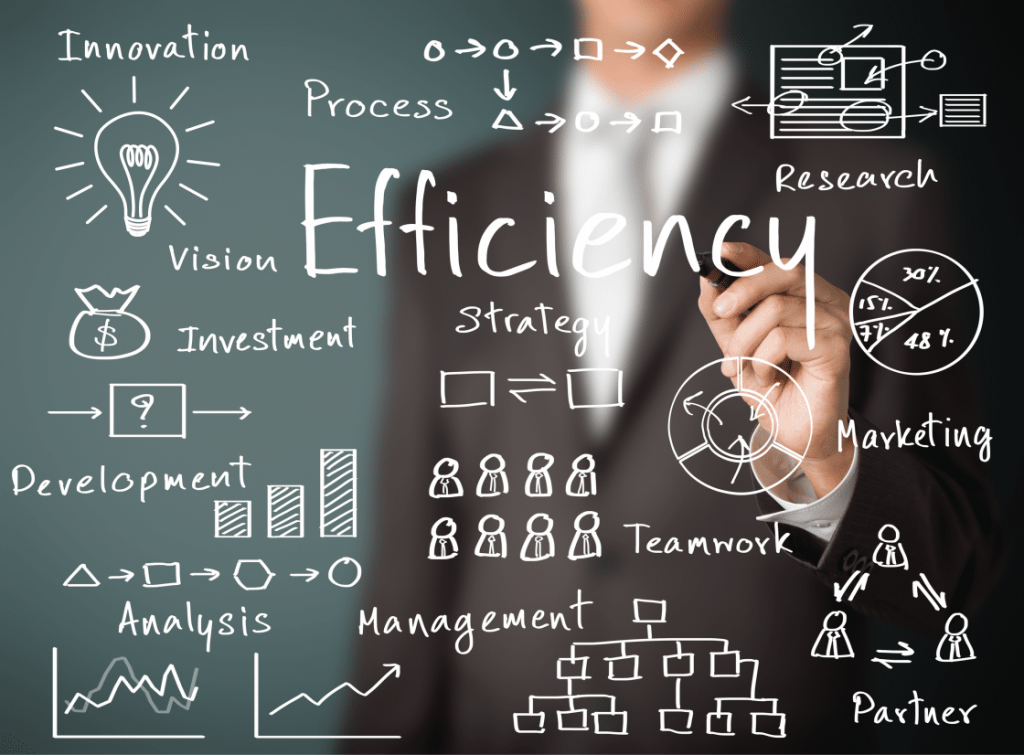
Next Level Growth
Firstly, conducting a BPE will provide a baseline of exactly where a utility or company’s business practices currently are. Through a rating criterion, findings report, and subsequent scoresheet, the opportunities for improvement will become clear. A company can then make modifications to their business practices to reach the next level of efficiency and effectiveness.
Objectivity
As a manager, it may be hard to focus on the cause of an issue when you are immersed in it every day. Conducting a BPE will allow for an industry expert to look at a situation objectively and make the best-informed recommendations based on the BPE’s proven history of success.
Cost Reductions
A successful Business Practice Evaluation will help companies cut costs by simplifying and refocusing existing business practices. Expert BPE consultants can look at costs from a different lens and offer insights based on data and effective-practice knowledge.
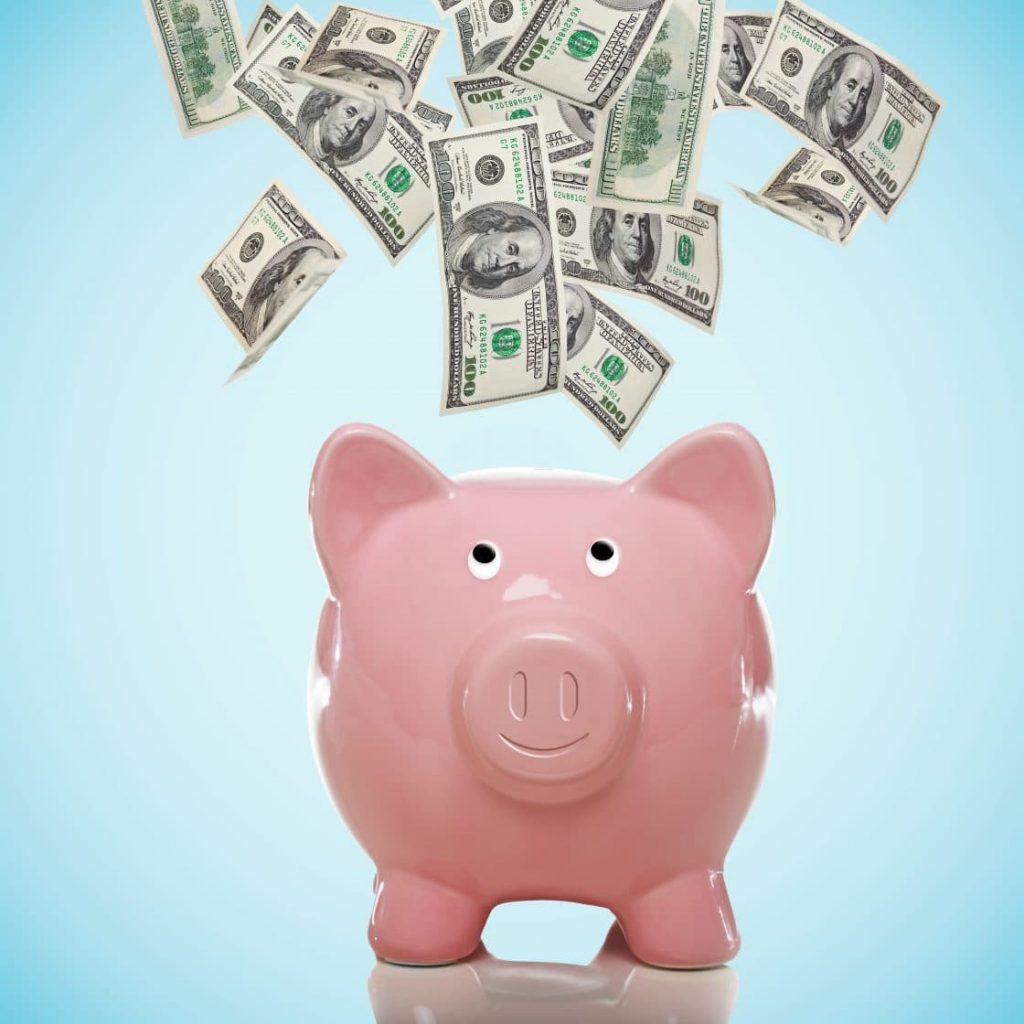
Improved Communication and Relationships
In big and small companies alike, communication is key. An open line of communication is particularly critical between management and field personnel in water and wastewater utilities. Through field observations of current business practices, valuable insights in reference to efficiency and effectiveness will be provided. Management and field personnel can then identify and prioritize opportunities for improvement, as well as come to a consensus in all business practices. A successful BPE will help to eliminate the fissure between management and field staff, eliminating the ‘us versus them’ mentality.
Staff Accountability
A Business Practice Evaluation is completed through a series of interviews within a diagonal slice of utility staff. Recommendations from the BPE findings report will aid in staff accountability by identifying and implementing realistic performance measures. For example, the report may show within the Administration category that an Emergency Response Plan (ERP) is not in place. Subsequently, a Public Water Supplier could then take the necessary steps to implement an ERP and provide staff with the required ERP training.
A Way Forward
One of the most valuable pieces of information obtained from conducting a BPE is knowing where a business stands from a micro-level view. Once the scoresheet is complete, a company can determine if their primary business functions are being efficiently and effectively managed (or not). Moreover, the risks and consequences of not moving forward with proposed recommendations are identified. Having this information allows management the ability to prioritize business practices and supporting attributes, and sets the business on the right path going forward.
Improved Quality of Life
Changes resulting from the completed Business Practice Evaluation have the potential to improve quality of life and staff morale by communicating and providing a clear management plan to move forward. While improvements may not always be evident prior to the BPE, management and staff alike will be happy when positive changes are made. With more efficient and effective business practices and improved communication, the business continues to thrive.
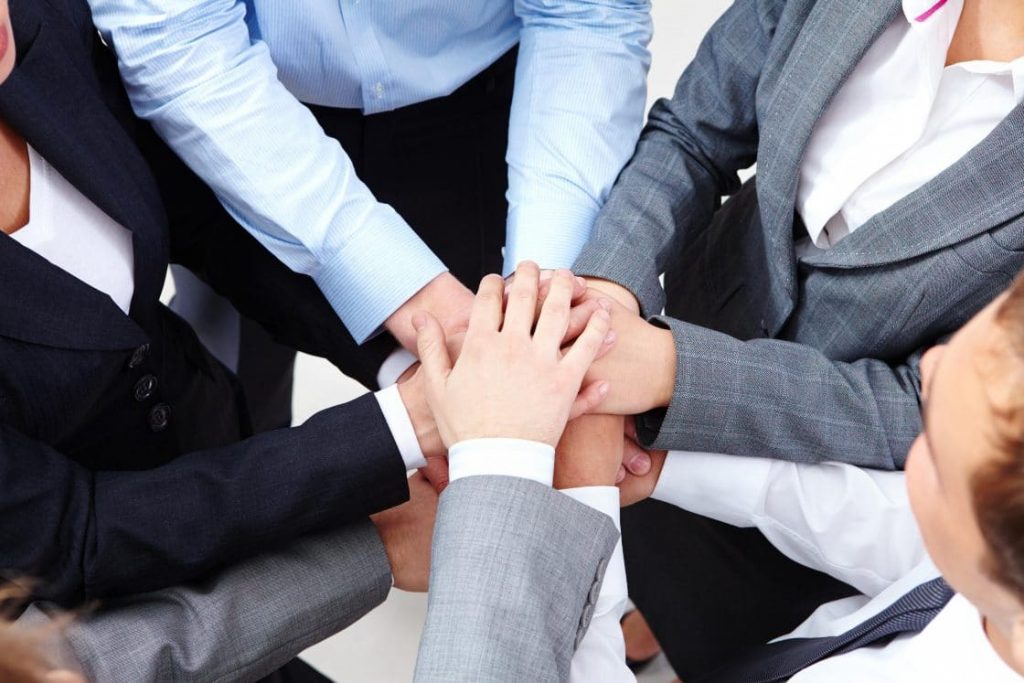
Interested in the full scope of the Business Practice Evaluation? See the step-by-step process below.
- Review utility documents and documentation of business practices
- Develop rating criteria to determine level of performance of business practices
- Develop business practice categories and supporting attributes scoresheet with the assistance of your utility staff
- Conduct kick-off, consensus, and findings workshops
- Conduct interviews within a diagonal slice of the organization
- Conduct field observations of current business practices (not people)
- Develop a BPE findings report
- Develop a BPE scoresheet from the findings report
In conclusion, it is critical to stay on top of internal functionality regardless of the type of business you operate. Keep in mind, no matter how well-oiled a machine is, there is always room for growth and improvements. Organizations that have conducted a BPE significantly improve the management, operations and maintenance efficiency of their utility.