In recent years, water systems have been faced with challenges that are unique to modern times. Our nation’s buried infrastructure is reaching a critical juncture in that it is nearing or has reached the end of its useful life, or is in dire need of replacement due to the presence of lead. At the same time, climate change is affecting supplies, while a burgeoning population is creating a larger demand. And as we increase our knowledge about the dangers of additional contaminants in our drinking water, utilities are saddled with increased regulations that require strict compliance by specific deadlines. Obtaining compliance often requires extensive upgrades or completely new infrastructure, all of which come with a high price tag.
And therein lies the problem. While water systems are facing such a complex set of challenges that require significant expenditure, available capital is quickly drying up. Water systems are seeing their budgets slashed while operations and maintenance costs soar. In addition, funding sources have been dwindling, and President Trump’s 2018 budget aims to slash them even further. In fact, Trump’s proposed 2018 budget completely eliminates the United States Department of Agriculture (USDA) Rural Development Water and Waste Disposal Loan and Grant Program. This program “provides funding for clean and reliable drinking water systems, sanitary sewage disposal, sanitary solid waste disposal, and stormwater drainage to households and businesses in rural areas who are not otherwise able to obtain commercial credit on reasonable terms.”1 In other words, lower income rural communities who fully rely on USDA Rural Development grants to fund their water system improvements will no longer have a source of federal funding.
The proposed 2018 budget also budget cuts the Environmental Protection Agency (EPA) by 31%, or $5.7 billion. The EPA provides funding to water systems through its Drinking Water State Revolving Fund (DWSRF) and Clean Water State Revolving Fund (CWSRF) programs, both of which “provide communities a permanent, independent source of low-cost financing for a wide range of water quality infrastructure projects.”2 Considering that almost all spending on critical infrastructure such as drinking water, wastewater, and transportation is provided by the public sector, these cuts are expected to make a huge impact on available funding for critical water infrastructure projects.
Because working capital is becoming so scarce, it is critical that water systems manage their assets with an eye on efficiency and systematic planning. Asset management is arguably one of the most important strategies for effectively maintaining utilities today and critical to the health and maintenance of water systems. Key components of a utility asset management plan include performing an inventory and condition assessment of the system’s assets, defining level of service goals, identifying critical assets, establishing life cycle costs, and developing a long-term funding strategy. In other words, a successful asset management plan requires a thoughtful, systematic approach that provides for the rehabilitation and replacement of assets over time, while also maintaining an acceptable level of service for existing assets.
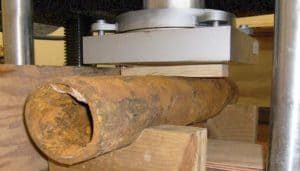
Today’s stringent budgets demand precise efficiency and cost-effectiveness, and determining which assets should be prioritized can be a challenge. It is no longer economically feasible to create an asset replacement schedule based solely on life cycle and critical components; rather, utilities today must pinpoint assets that are most in need of repair or replacement in order to stretch existing capital and justify new budget requests.
Capital efficiency planning helps to do just that. Our proprietary Capital Efficiency Plan™ (CEP) methodology combines the concepts of asset management, hydraulic modeling, and system criticality into a customized, comprehensive report that provides utilities with a roadmap for future repair and replacement. The report includes database and GIS representation for each pipe segment within their underground piping system, prioritizes water distribution system piping improvements, and provides estimated costs for water main replacement and rehabilitation. Because each water system has unique characteristics and challenges, our CEP includes a workshop with knowledgeable field staff and managers for each project that helps to fill in data gaps, correct incorrect records, and identify specific issues and critical components that are custom to the system. The results of the workshop provide significant value by improving the quality of the asset data and the accuracy of the hydraulic model. Because the CEP utilizes a highly structured, detailed, and targeted approach, utilities can confidently justify the costs of repairing or replacing those assets most in need of repair or replacement when preparing annual budgets. Our CEPs have assisted numerous utilities throughout New England by providing a practical and easily understandable plan to critical asset repair and replacement, as well as an advantage when it comes to procuring funding. The same approach can be applied to above ground assets as well as wastewater and stormwater systems.
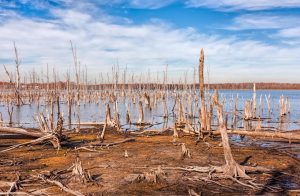
Increasing regulations, climate change, shrinking budgets, dwindling supply, and population growth — these are all challenges that affect the financial capacity of today’s utilities. And with the proposed budget cuts under the Trump administration, water systems will feel even greater fiscal pressure. Competition for SRF funding will intensify, and utilities will be required to definitively justify the reason for their funding request. By combining asset management with hydraulic modeling and system criticality, our Capital Efficiency Plans™ can help utilities to maintain the health and viability of their water systems today so that they can continue to provide safe, clean drinking water tomorrow, and well into the future.
1 rd.usda.gov
2 epa.gov