Since many EOs were at the corporate office in Marlborough, MA for training on September 20, the ESOP Committee decided to host an after-hours Poker Night complete with barbecue from Firefly’s and a variety of beers including fellow ESOP Harpoon Brewery’s Flannel Friday. EOs enjoyed some great food and downtime while also participating in a friendly Texas Hold’Em tournament. The grand winner of the night was Dave Ceppetelli from the Vermont office, and he walked away with a VISA gift card. The response from the team was extremely positive, and we can’t wait for the next fun outing (which will be very soon considering October is ESOP Month!)
Month: September 2017
Shared WW Treatment Facility Improvements Whitepaper
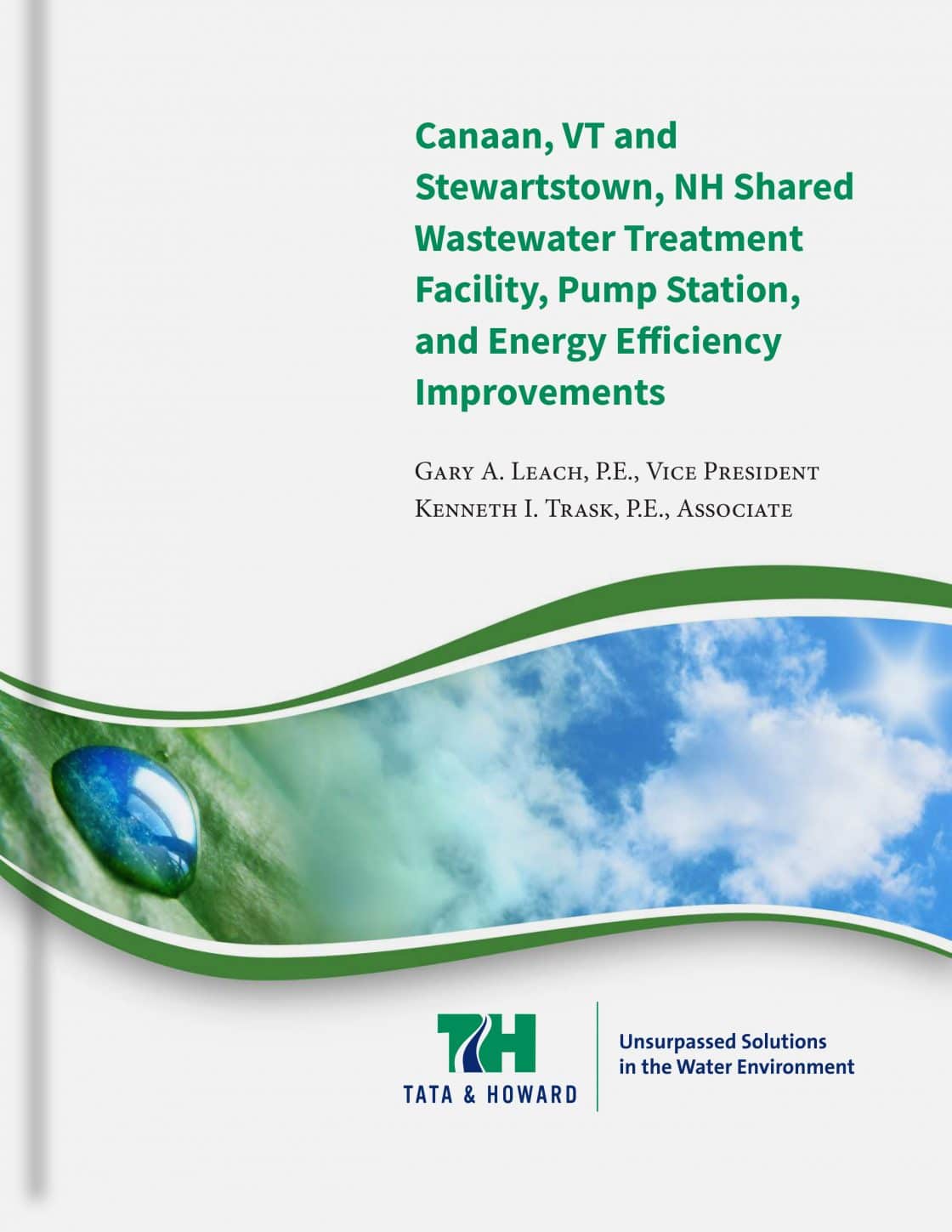
Abstract: The Towns of Canaan, Vermont and Stewartstown, New Hampshire operate a shared wastewater treatment facility, which required significant upgrades. The existing facilities were 40 years old and although a few upgrades were performed in the 90s, the facilities were not performing well, did not meet Life Safety codes, and required significant maintenance. The economical upgrade met all of the goals of the Client by providing for simple operation and maintenance requirements, meeting the Life Safety codes, eliminating confined spaces, lowering of electrical power costs, and meeting discharge parameters through production of high quality effluent.
Pollution Prevention Week – Tips for a Greener Future
Pollution Prevention Week takes place each year during the third week in September. This special week celebrates the passing of the Pollution Prevention Act in 1990, and serves as an opportunity for businesses, individuals, governments, organizations, and groups to focus on pollution prevention (P2) by celebrating their sustainability achievements, expanding current practices, and implementing new initiatives. In addition, P2 Week serves to remind individuals and organizations of the myriad ways that pollution can be prevented.
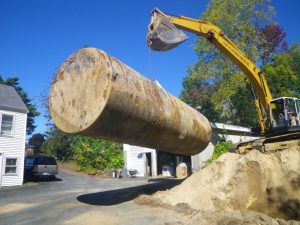
While many organizations and initiatives focus on recycling and mitigation, the most efficient and beneficial way to protect the environment is to avoid pollution in the first place. Once the environment has been compromised, it is much more labor intensive, energy intensive, and costly to return conditions to their natural state. For example, ensuring that double-walled Underground Storage Tanks (USTs) are maintained and in good condition is critical to the protection of groundwater and soil. When a UST leaks and contaminates the surrounding area, soil remediation is required, which in some cases can cost hundreds of thousands of dollars. In addition, any contaminated water will require a much more comprehensive treatment train, leading to expensive infrastructure projects and higher operational costs for water utilities. Preventing the leak in the first place requires simple maintenance and monitoring, such as regular testing of leak detection systems, maintaining accurate inventory records, and maintaining spill buckets, which comes at a small fraction of the cost of clean-up activities to both the wallet and the environment.
Pollution prevention is just as important on an individual level. While the actions of one person may seem insignificant, the collective action of millions of individuals is monumental. In celebration of P2 Week, we’ve assembled 20 simple tips that we can all implement to minimize our environmental footprint.
- Make sure your home is well-insulated and has energy efficient windows.
While not practical for everyone, chickens provide grub control, aeration, and fertilization for lawns. - Practice environmentally-friendly lawn care (Here are 10 tips to start!)
- Use water-based paints and be sure to rinse paint brushes in the sink, where the water will eventually make its way to a wastewater treatment plant, and not outdoors, where the paint will end up in the groundwater.
- Utilize LED lights instead of fluorescents, which may contain mercury. When disposing of fluorescent bulbs, be sure to take them to a certified collection center.
- Plant trees. They help to keep the air clean.
- Utilize recycled content plastic lumber for decks. Plastic lumber lasts far longer than wood lumber and requires no painting.
- Fix leaks and install water saving faucets and fixtures. (Visit here for more water tips!)
- Compost kitchen scraps with worms. Bonus: you’ll get free, organic plant food.
- Always bring reusable bags to the grocery store. Worldwide, we throw away over one trillion plastic bags each year, many of which end up in our oceans.
- Buy products in the highest bulk possible to avoid excess packaging.
- Use non-toxic household cleaners and personal care products.
- Dispose all prescription drugs at a certified drop-off location. Do not flush! Prescriptions are wreaking havoc on our water supply.
- Use cloth napkins instead disposables, and washable rags instead of paper towels.
- Buy organically grown food. Pesticides contaminate our water and harm our environment.
- Use reusable glass containers for leftovers and lunches. Avoid plastic baggies and boxes.
- Lower household heat by a degree or two, and have the boiler serviced annually to increase efficiency.
- Be sure appliances are energy and water efficient, and only run the dishwasher and clothes washer with full loads.
- Carpool, walk, or bike to work, or use public transportation. If possible, work at home one day per week to save fuel and energy.
- Buy washable clothing that doesn’t require dry cleaning. Dry cleaners are a large contributor to environmental contamination.
- Use rechargeable batteries, and be sure to dispose regular alkaline batteries at a certified drop-off location. Batteries can wreak havoc on our soil.
Do you have any other easy tips to prevent pollution? If so, share them in the comments. As Vincent Van Gogh said, “Great things are done by a series of small things brought together.” At Tata & Howard, each of us looks forward to creating a greener, healthier future by doing our individual, small part to decrease pollution. Happy Pollution Prevention Week!
Not Just for Manufacturing — Lean Techniques for Water and Wastewater Utilities
The term “Lean” has become widely used in the manufacturing sector since the late 1980s when it was first used by James P. Womack, Ph.D. of MIT’s International Motor Vehicle Program to describe Toyota’s highly successful manufacturing process and business model. While its core premise of eliminating waste is quite simple, identification of waste and implementation of best practices takes effort. Waste can be defined as any process or activity without value — such as overproduction, defects, and waiting — and accounts for up to 60% of a typical manufacturing company’s production activities.
But Lean isn’t just for manufacturing companies. In fact, most companies can benefit greatly from incorporating Lean techniques into their standard operating procedures. At its core, Lean enables a business to run more efficiently by improving quality and reducing costs, whether that company is a car manufacturer, a hospital, a retail operation — or even a water or wastewater utility.
Key Principles
The Lean Enterprise Institute (LEI), long considered the premier resource for lean theory and training, identifies the five key Lean principles as value, value stream, flow, pull, and perfection. Value is always defined through the customer, and addresses such issues as price point, delivery timelines, requirements, and expectations. Value to a water or wastewater utility may include price, quality of water or effluent, reliability of service, and meeting regulatory requirements.
Once value has been established, each and every step and process taken to meet that value is mapped as the value stream. These steps include not only manufacturing processes, but also contributing areas and departments including administrative, human resources, and customer service. By mapping every step in the process, identification of areas lacking value can be identified and addressed. Value streaming results in not only less waste, but also improved operational understanding.
Flow refers to process efficiency and is the next step after waste was been eliminated from the value stream. Often, creating true flow requires cross-functionality across departments, something that can be a challenge for companies to implement. However, this step also boasts some of the highest efficiency gains. For water and wastewater utilities, increasing flow may include moving towards transparent communication between operators and management and standardization and documentation of processes and effective practice guidelines. Ensuring that the remaining steps in the process occur smoothly and without interruption is key to the lean process.
Reducing waste in the value stream and improving flow enables a manufacturing company to shorten the manufacturing process and implement “just in time” delivery, or pull. In service operations such as water and wastewater systems, pull focuses on the people and refers to the way in which work is distributed and managed. In a traditional push system, all projects and tasks are distributed as a giant to-do list, which can lead to disorganization, diluted priorities, and employees feeling overwhelmed. In a pull system, workers are allowed to pull in tasks as they are ready, leading to a more focused approach to projects, better prioritization of key initiatives, and increased communication between workers at all levels. Organizations that utilize a pull system for work realize a significant reduction in wasted time resulting in far more efficient time utilization.
The final step may actually be the most important: perfection. Perfection refers to continuous improvement by incorporating Lean thinking into the very fabric of the corporate culture. Perfection acknowledges that true Lean requires constant effort and is never static.
Lean Implementation
Because the main goal of Lean is to create more value with fewer resources, a Lean company strives to create an organization that provides perfect value with zero waste. In addition to changing from silo to matrix management, implementing Lean follows four basic tenets, known as the four Ps of Lean thinking: purpose, process, people, and performance.
Purpose
Companies must first determine their essential purpose. For some companies, profit may be the driving motivation, while others may exist for philanthropic purposes. Water and wastewater utilities provide an essential service to customers. Besides the general purpose of the organization, a company must also determine its philosophical drivers. These can include core values, mission, and vision.
Process
Once purpose has been determined, a company must determine the process by which it reaches its customer and produces the product, whatever that product may be. Simply put, process refers to the way in which a business operates in relation to its customer and its internal operations. Most of the key principles of Lean thinking can be applied during the process step. Unfortunately, it is also the step at which many businesses become stuck if they lose focus or lack cooperation from employees or management.
People
People refers not only to those for whom the product or service is created, but also the people within the organization who create the product or service. In other words, people are customers and employees, as well as some consultants and suppliers. Developing employees, growing leaders, improving management, and showing respect at all levels are important facets of this critical step.
Performance
Performance is the final step of the Lean approach and is in line with the perfection principle. A company must assess any improvement in its ability to deliver its product or service, and identify any additional gaps. Lean implementation typically goes through many trials and iterations before truly successful performance is achieved. Again, it is critical to remember that Lean is a continuous process that requires vigilance and ongoing effort from an organization.
Lean Thinking in Water and Wastewater Operations
Because it is often referred to as lean manufacturing, there is a misconception that Lean is strictly for manufacturing organizations. In fact, Lean is not a set of tactics or a simple method of cost reduction; rather, Lean is a completely different way of thinking and operating on an organization-wide basis.
For water and wastewater, Tata & Howard’s proprietary Business Practice Evaluation (BPE) is a highly effective methodology that can assist utilities in becoming lean organizations. By definition, a BPE is a “process that assesses the health of a utility’s business practices with the goal of minimizing the total cost of managing, operating, and maintaining utility assets while delivering exceptional service to customers” — the core definition of lean thinking. A BPE accomplishes this by assessing all business practices, identifying opportunities for improvement, and implementing a framework for a structured approach to managing, operating, and maintaining a utility in the same manner as a profitable business, where focus is placed on management of resources, employee engagement, operational efficiency, and customer service. The finished product provides a utility with a clear understanding of baseline history and areas of opportunity for improvement. In addition, the utility receives a matrix of recommendations for each business practice they want to improve, along with the risk and consequence of inaction. Organizations that have conducted a BPE significantly improve the operational efficiency of their utility. A BPE is arguably one of the most important steps in a water or wastewater utility’s journey toward becoming a truly Lean organization.
In Conclusion
All types of businesses across all industries and service offerings are turning toward Lean thinking to remain competitive and profitable in today’s consistently changing corporate climate. Successful Lean organizations recognize that lean is not a one-time cost reduction program or a quick fix, but rather a completely different way of thinking and operating that constantly evolves. While true Lean transformation takes long-term vigilance and attention, the benefits of increased operational efficiency, exceptional customer satisfaction, and better profitability are well worth the effort.