Water Management Act/Sustainable Water Management Initiative (SWMI) Summary
Water Management Act (WMA) permits that expired between 2010 and 2015 were extended for four years by two Legislative Permit Extension Acts. Permit renewals are currently proceeding based on MassDEP’s schedule, although delays are expected. Basins with renewal applications on file will likely be extended, and correspondence will be sent. For renewals not yet on file, and particularly those not scheduled for renewal for several years, no determination has been made for extension.
Sustainable Water Management Initiative (SWMI) Requirements
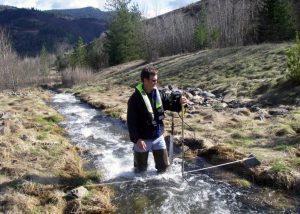
SWMI Sustainable Management Practices:
- Natural streamflow estimates
- Cumulative water balance picture
- Baseline water use
- Streamflow criteria, biological categories, and groundwater withdrawal categories
Demand Projections:
- MassDEP and DCR developed demand projections to be used as the basis for new permitted volumes for each PWS.
- In many cases, allowable withdrawal volumes are being reduced.
WMA Permit Conditions
Existing — Requirements All Based on Water Conservation
- Residential Gallons Per Capita Per Day (RGPCD) water use: 65 RGPCD
- Unaccounted-for-Water (UAW): 10%
- Leak Detection and Metering: 100% metering; annual master meter calibration; program to test all meters over 10 years old
- Pricing: Pricing system should reflect the full cost of supplying water; water supply system operations should be fully funded by water supply system revenues
- Plumbing: Enforcement of the March 1, 1989 plumbing code; retrofit all public buildings with water saving devices; make retrofit devices available to customers if RGPCD water use exceeds performance standard
- Education: Develop a public education program; include bill stuffers with water conservation tips or water saving messages to customers
New, Additional Requirements
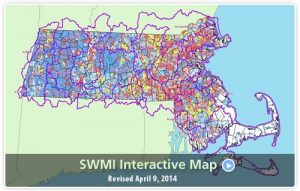
Baseline defined by MassDEP = higher of 2003-2005 average use plus 5%, or 2005 use plus 5%, provided that baseline cannot exceed the previous maximum authorized volume.
Mitigation programs required for systems using or requesting volumes greater than Baseline based on Tier classification of basin.
- Mitigation credits will be determined by MassDEP but recently watershed groups played a major role in approving credits allowed for Mitigation programs.
- Tier 2 and Tier 3 permittees must undertake mitigation commensurate with the impact of their increased withdrawals.
- Applicants that cannot avoid changing the Biological Category or Groundwater Withdrawal Category of a sub basin (backsliding) that have no feasible alternative sources will be required to implement the highest level of mitigation.
- A mitigation plan should estimate the required volume of mitigation, identify feasible mitigation options, and include a timeline for the implementation of the mitigation options.
Minimization: All tiers of permittees with withdrawals in subbasins having August net groundwater depletion of 25% or greater must minimize the impact of their withdrawals in those subbasins. The minimization plan must be approved by DEP and should reflect the following three analyses:
- Desktop Optimization: Evaluate whether the applicant’s existing sources, or any available alternative sources, could be utilized or operated at prescribed rates or times in a way that could reduce environmental impacts while still meeting water demands.
- Water Releases and Returns: Evaluate releases from surface water supply impoundments and measures that could return water to the subbasin or basin to improve flow.
- Additional Conservation Measures: Evaluate reasonable and cost-effective indoor and outdoor conservation measures consistent with public health and safety that go beyond standard WMA permit conditions.
Coldwater Fishery Resource (CFR) Protection: All tiers of permittees with withdrawals that impact streamflow at a CFR must evaluate reducing impacts to CFRs through a desktop optimization. Tier 2 and Tier 3 applicants must evaluate further protection of their CFRs as part of their required mitigation planning.
Alternative Source Analysis: Tier 3 permittees must show that they have no feasible alternative source that is less environmentally harmful.
Outdoor Water Use Restrictions: New outdoor water use restrictions will be required based on streamflow and or groundwater conditions, basin criteria and PWS compliance with performance standards. Limits include watering one or two days per week, no watering 9am to 5pm.
For more information on the SWMI final framework, please visit MassDEP’s website here. For questions or assistance with SWMI or WMA, please contact us.